Pressure gauges should be installed in areas with minimal heat, vibration and moisture exposure for accurate readings. Stem-mounted and flush-mounted rear-connected gauges are available to best suit your needs. Easy installation ensures an accurate reading, so ensure the pressure gauge is placed in an easily accessible and visible location. Whichever style you choose, ensure the dial can be easily read.
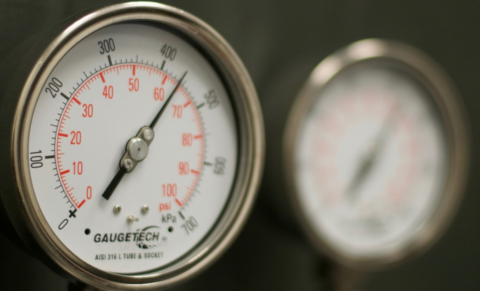
Ambient Temperature
How Temperature Affects Pressure Gauges
Pressure gauges should preferably be used at an ambient temperature between –20 and +150°F (–30 to +65°C) to ensure the long life and accuracy of the product. Standard gauges may exhibit a slow pointer response at shallow temperatures. Above 150°F (65ËC), the accuracy will be affected by approximately 1.5% per 100°F (38ËC). In addition, the pressure gauge should not be used outside of its rated temperature limits, as noted on the Data Sheet specific to that gauge. If you use it at temperatures above or below these limits, the gauge accuracy will be significantly reduced, and the possibility of gauge failure may exist.
Corrosive Process Media
Or High Temperatures
To prevent hot media such as steam from entering the bourdon tube, a gauge siphon or pigtail filled with water should be installed between the gauge and the process line. A cooling tower may also be used to reduce the temperature effect on gauges. If corrosive media or media that will plug the instrument is present, a chemical or a diaphragm seal made of stainless steel or other exotic materials should be used to protect the wetted parts.
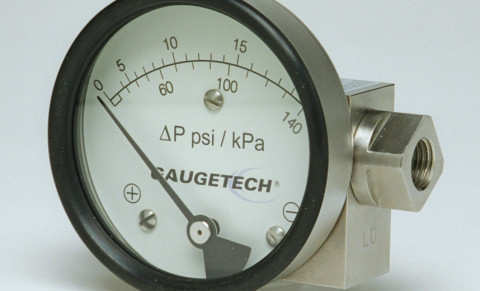
Isolating Devices
A shut-off valve such as a needle valve or gauge cock should be installed between the gauge and the process in order to be able to isolate the gauge for inspection or replacement without shutting down the process. The use of such devices are critical in times where start up pressures may temporarily exceed normal operating pressure. All isolating devices shall be opened slowly to prevent “slamming” of the bourdon tube. Care not taken during this time may damage the instrument.
Overload Protection
An overload protector should be used in situations where the process media may spike or be susceptible to overpressure of the design range for the gauge. This will prevent damage to the instrument.
Threaded Connections
The tightening or loosening of gauge connections can be done using the wrench flats on the gauge fitting. Using the gauge case to tighten or loosen pressure gauges will damage the gauge and may cause unrepairable damage to the instrument. Proper sealant tape or paste should be used for sealing tapered threads like National Pipe Thread (NPT)
Vibration / Pulsation Protection
If the pressure gauge is exposed to vibration or pulsating pressure or both, a liquid filled pressure gauge is recommended. The liquid dampens the effects of vibration making the pointer easier to read. Pressure dampeners, snubbers and or restrictor screws may be used to reduce pulsation. In extreme cases, a remotely mounted liquid filled gauge connected with a length of capillary line may be used.